Качество композитных конструкций
Повысить качество плоскостных элементов конструкций из композиционных материалов (КМ), изготавливаемых способами послойной выкладки с последующим прессованием при повышенной температуре, можно только применяя специальные технологические приемы. Один из приемов связан со способами реализации натяжения наполнителя из ткани или волокна при изготовлении силовых агрегатов летательных аппаратов. Другой прием позволяет осуществлять одновременный прогрев материалов на внутренней поверхности при переменной толщине композита в конструкции, тем самым обеспечивая тепловой режим в технологическом процессе полимеризации и, следовательно, качество изделия.
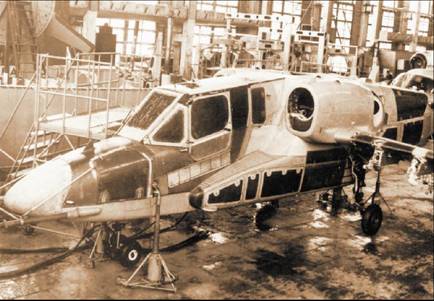
Известно, что наилучшими свойствами композиционные материалы обладают в конструкциях, которые изготавливаются методом непрерывной намотки. В этом случае обеспечиваются оптимальные режимы укладки слоев с необходимым натяжением волокон, что и обеспечивает материалу максимальные механические свойства. Однако для силовых плоскостных деталей планера самолета и вертолета типа лонжеронов, нервюр, обшивок используемая технология изготовления и соответствующая ей технологическая оснастка не обеспечивают необходимое натяжение волокон, что приводит к существенному снижению свойств материала. Это снижение свойств прогрессирует с увеличением толщины материала, так как в этом случае при прессовании изделий сильнее сказывается отклонение волокон от прямолинейной формы. Кроме того, при отсутствии натяжения надавливание волокон соседних слоев, уложенных под разными углами, приводит к дополнительному их искривлению по отношению к необходимому направлению. Недостаток, имеющий место в используемых способах изготовления деталей, можно устранить, если использовать прием натяжения волокон в слоях с различными углами укладки. Поэтому разработка новых технологических приемов и совершенствование известных методов повышения качества композитных изделий способствуют снижению массы и увеличению надежности конструкции.
Прием натяжения волокон на примере лонжеронов крыльев самолета рассматривался довольно часто. Однако, в основном, речь шла о натяжении волокон, преимущественно имеющих направление ±45°-90° в поперечном сечении стенки лонжерона. Так как лонжерон является основным силовым элементом крыла, воспринимающим изгибающий момент, то толщина полок может достигать существенных величин. Это скажется на распределении напряжений по толщине, на плотности структуры при прессовании и на межслоевой прочности. Сложнее всего осуществить натяжение продольных волокон полок лонжерона, которые являются основными нагруженными элементами. От их свойств и качества зависит работа крыла в целом. Эта процедура несколько упрощается при изготовлении элементов из препрега, когда связующее находится в полуотвержденном состоянии. Рассмотрим вариант разработки технологической оснастки для производства длинномерных силовых элементов и некоторые рекомендации по ее изготовлению.
Особенность проектирования пресс- форм, в которых изготовление деталей осуществляется с натяжением волокон, связана с необходимостью учета термического удлинения материала, увеличением размера детали при натяжении волокон, обеспечением подвижности некоторых частей оснастки, изменением объема материала, создающего давление прессования. Для конкретизации рассуждений приведем схемы сечений пресс-формы вместе с изготавливаемой деталью (рис.1).
Корпус пресс-формы определяет габариты детали. Давление на поверхности композитной детали создается двумя путями. Резиновый мешок (2) с помощью сжатого воздуха создает необходимое давление на наружных поверхностях полок лонжерона. На стенки лонжерона давление передается резиновой мембраной (7) также с помощью сжатого воздуха. Резиновая мембрана приклеена к металлическому вкладышу (8) по горизонтальным полкам. В этом случае резиновая прокладка создает давление на внутреннюю поверхность полок лонжерона за счет термического расширения самой прокладки и создания распорного усилия между подвижным элементом пресс-формы (6) и металлическим вкладышем (8). Величина распорного усилия должна быть достаточной для обеспечения натяжения в стенке лонжерона и в то же время не превышающей допустимого давления на поверхности композита. Величина давления регулируется толщиной резиновой мембраны на горизонтальном участке, которая может быть рассчитана с учетом совместной работы резины и стенки лонжерона.
В настоящее время в пресс-формах используется резина марок ИРП-1338, ИРП-1400, герметики У-1-18, У-2-28 и другие материалы. Положительные результаты дает применение силиконовой резины для создания давления в замкнутом объеме за счет ее терморасширения при нагревании. Имея небольшой модуль упругости (Е=180 МПа), она обладает высоким коэффициентом линейного термического расширения (n=250Ч10-6 1/град.), что в замкнутом объеме позволяет создавать необходимое давление или усилие. Это свойство позволяет использовать силиконовую резину для создания деформации растяжения в материале полки.
Рассмотрим один из способов создания такого натяжения в мощных силовых лонжеронах, позволяющий учитывать возможные изменения ширины и толщины полки лонжерона. На рис.2 приведена схема реализации растяжения полки в процессе технологического нагрева и сохранения части такого растяжения после охлаждения приспособления (эта схема соответствует сечению А-А рис.1).
Полка лонжерона с одной стороны испытывает давление резинового мешка (2), а с другой – резиновой прослойки мембраны (7). В таких условиях при перемещении металлических прокладок (3) и (6) за счет сил трения на ее поверхности образуется растяжение материала. Эффект проскальзывания металлических прокладок (3) и (6) и создание натяжения усиливаются при использовании разрезов резиновых элементов (9), которые приклеиваются только к одной прокладке (3) по торцевой стороне. Прокладки (3) и (9) удлиняются и перемещаются относительно стенки (10), расположенной посередине длины приспособления. Так как резина имеет большой коэффициент термического расширения, при охлаждении всей конструкции происходит ее усадка, между прокладками образуются зазоры, а в полках лонжерона сохраняется растяжение, пока сохраняется давление в резиновых камерах (2) и (7). Все необходимые размеры прокладок рассчитываются в зависимости от габаритов и жесткости изготавливаемого изделия.
Еще один метод повышения качества композитного изделия предполагает обеспечение равномерности прогрева структуры по толщине стенки вдоль ее длины. Эта задача особенно трудно выполнима, когда толщины стенок конструкции существенно меняются по площади изделия. В этом случае при постоянном притоке тепла на поверхность элемента не будет выдержан температурно-временной режим процесса полимеризации в каждой точке объема, что может отразиться на свойствах и качестве изделия. В большинстве случаев регулирование теплового потока по поверхности конструкции осуществить невозможно из- за сложности и дороговизны реализации этого регулирования. Кроме того, перечисленные особенности трудно поддаются учету при расчете и проектировании технологической оснастки.
Существует конструктивный прием, который обеспечивает такой процесс изготовления, при котором в каждой точке материала реализуется заданный технологический режим. Желательно, чтобы коэффициенты термического расширения изделия и приспособления были одинаковыми. Проще всего качество изделия с переменной толщиной стенки можно обеспечить, если на поверхность изделия класть фиктивный материал, толщина которого должна меняться в зависимости от толщины материала конструкции таким образом, что бы их суммарная толщина была постоянной по всей поверхности изделия. В этом случае отпадает необходимость регулирования теплового потока по поверхности технологического приспособления, что позволяет обеспечить одновременное достижение необходимой одинаковой температуры на внутренней поверхности изделия в случае одностороннего нагрева.
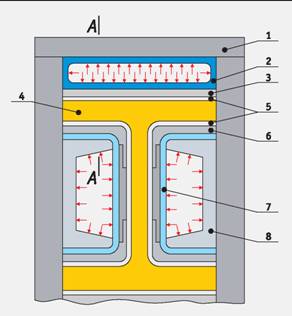
Рис. 1. Поперечное сечение пресс-формы с изделием
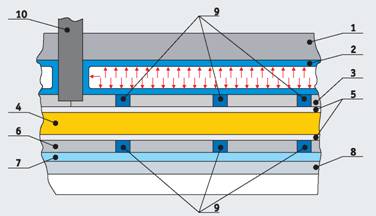
Рис. 2. Продольное сечение пресс-формы с изделием
На рисунках 1 и 2 цифрами обозначены: 1) корпус пресс-формы; 2) резиновый мешок для создания давления; 3) металлическая прокладка; 4) композитная деталь; 5) прокладки из фторопласта; б) подвижные элементы пресс-формы; 7) резиновая прослойка мембраны; 8) металлический вкладыш; 9) резиновые элементы (вкладыши); 10) стенки пресс-формы
Расчет напряженно-деформированного состояния конструкции показывает, что при использовании фиктивного материала деформации укладываются в рамки допускаемых отклонений.
Александр ДУДЧЕНКО, докт. техн. наук профессор,
Вячеслав РЕЗНИЧЕНКО, канд. техн. наук доцент, МГТУ (МАИ)
ЭКСПЛУАТАЦИЯ
Более 800 000 книг и аудиокниг! 📚
Получи 2 месяца Литрес Подписки в подарок и наслаждайся неограниченным чтением
ПОЛУЧИТЬ ПОДАРОК