Композитные лопасти: Часть 2 выкладка или намотка?!
Основания выбора технологии
Выбор технологии, которая затем обусловливает конструкцию, зависит, прежде всего, от того, как решается проблема соотношения технологичности, определяющей себестоимость изделия, и стабильности физических характеристик.
Существует стереотипная точка зрения, согласно которой укладочная технология предполагает большое количество ручных операций, а значит, более низкую стабильность и более высокую стоимость. Считается также, что при намоточной технологии основные операции механизированы, следовательно, обеспечиваются более высокая стабильность и более низкая стоимость. Однако выяснилось, что при изготовлении лопастей несущих винтов складывается диаметрально противоположная ситуация.
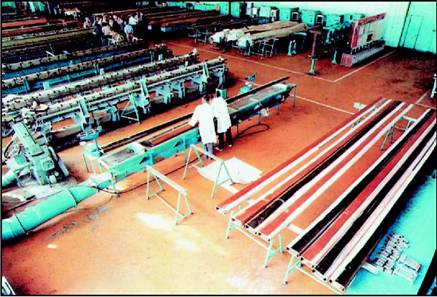
Производство лопастей на КумАПП
Мы уже говорили, что за механизацию формирования дельтовидного лонжерона пришлось «расплачиваться» снижением прочности и значительной нестабильностью характеристик. И тем не менее, вполне автоматизированным процесс все же не получился, так как структура композита, отвечающая полетным условиям, не позволяет получить удовлетворительные характеристики ползучести. Оказалось, что со временем на стоянке деформации лопасти недопустимо нарастают, и это обусловливается не столько свойствами волокон, сколько характеристиками ползучести связующего, которые значительно ниже соответствующих характеристик волокон. Поэтому приходится время от времени прерывать процесс намотки и укладывать волокна вдоль лонжерона, чтобы обеспечить приемлемые характеристики ползучести материала.
Известно, что механизация процесса намотки всегда рассматривалась как преимущество данной технологии. Но, как мы видим, и эту операцию полностью механизировать не удалось.
Оценим по вышеуказанным критериям (технологичность и стабильность) укладочную технологию. Для обеспечения стабильности конструкции чрезвычайно важно, чтобы нити располагались в строго определенных направлениях. Необходимо также избегать появления складок – главного повреждающего фактора. Можно предположить, что при ручной укладке существует риск снижения качества изделия. Однако уже достаточно давно разработаны приемы и приспособления, растягивающие и разглаживающие лоскуты препрега или тканей и избавляющие их от складок. Эта же задача решается использованием технологии, при которой давление подается изнутри в сторону наружного контура. В результате укладочная методика оказывается более толерантной к отклонениям, чем намоточная.
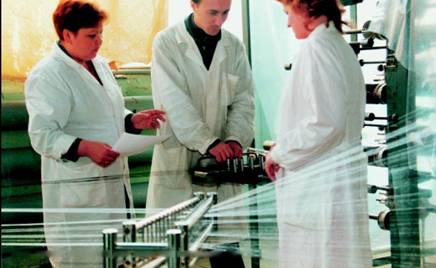
Подготовка препрега для лопастей вертолета Ми-38 (КВЗ)
Таблица 1
Вертолет Изготовитель Тип лопасти Стоимость серийного комплекта Вес комплекта n*G, кг Назначенный ресурс, ч Стоимость 1 кг сегодня, $ США Стоимость 1 кг/ресурс $ США/R * 10-3 Ми-2 Польша металлические 17000 $ США 3x57 2200 ~100 ~45 Ми-8 Казань/Улан-Уде металлические 60000 $ США 5x140 2000 ~85 ~43 Ми-26 Ростов-на-Дону основа металлическая + композиты ~300000 $ США 8x395 1200 ~95 79 Ми-24 Ростов-на-Дону металлические ~ 50000 $ США 5x116 1200 ~86 ~72 Ка-32 Кумертау композитные,укладка 100000 $ США 6x70 3000 238 ~79 Ми-34 Москва композитные, намотка 22000 $ США 4x15 600 366,6 611Не нужно думать, что производство композитных лопастей на основе укладочной технологии не имеет проблем. Лопасти вертолетов создаются в технологически сложных условиях, несоблюдение которых ведет к возникновению ряда серьезных проблем. Могут возникнуть явления непропрессовки и (или) перепрессовки пакетов, отклонения от требуемого «дрейфа» слоев ткани в процессе прессования и даже складки, что недопустимо. Однако в отличие от намоточной технологии здесь отсутствуют генетические, неустранимые дефекты.
Конечно, сравнительный анализ обеих технологий требует большего количества информации. Мы обладаем лишь некоторыми итоговыми данными, которые и приведем ниже. Безусловно, нельзя говорить о том, что использование намоточной технологии вообще недопустимо при изготовлении лопасти с лонжеронами. При умеренных нагружениях, которые возникают в процессе эксплуатации серийных транспортных вертолетов в режиме обычных скоростей, такие лопасти могут оказаться достаточно долговечными. Однако можно ли считать этот довод убедительным при решении вопроса о целесообразности их производства?
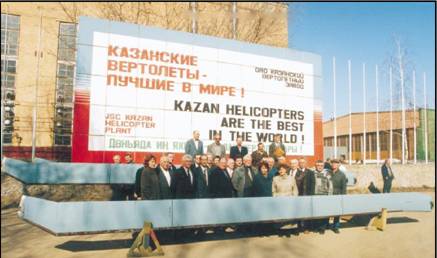
Первый летный комплект лопастей для Ми-38 (КВЗ)
Практическая целесообразность
Предположим, что цена лопастей в настоящее время определенным образом коррелируется с их себестоимостью. Правда, при существовавшей ранее системе исключения затрат на создание и внедрение новой технологии из стоимости серийной продукции представление о себестоимости было несколько искаженным. Тем не менее, в первом приближении цена изделия дает некоторое представление о технологичности процесса.
Однако для оценки эффективности технологии показатель собственной стоимости конструкции недостаточен. Необходимо ввести новый комплексный показатель – отношение удельной стоимости конструкции к ресурсу. Благодаря этому показателю можно оценить, сколько стоит один час эксплуатации одного килограмма конструкции, и сравнить изделия с разными конструктивными параметрами (вес, размер, ресурс). Выразим это формулой
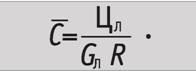
В табл.1 приведены характеристики различных лопастей – как композитных, так и металлических. Вертолет Ми-26 эксплуатируется уже свыше 20 лет. И это единственная серийная машина с лопастями рулевого винта, созданными по намоточной технологии. В настоящее время они имеют ресурс 1200 часов, а цена эксплуатации одного килограмма композитных лопастей в течение часа составляет приблизительно $ 0,25. При этом наружный контур лопасти Ми-26 не формируется жесткой пресс-формой, то есть лопасть лишена одного из «генетических» дефектов.
Из таблицы следует, что цена эксплуатации одного килограмма металлических лопастей средних транспортных вертолетов в течение часа составляет приблизительно $ 0,045, для вертолета Ми-26 – примерно $ 0,08. Эксплуатация композитных лопастей, изготовленных по укладочной технологии, обходится в $ 0,079 (килограмм на час ресурса), т.е. практически не отличается от цены эксплуатации металлических лопастей.
Как видно из таблицы, эта цена для лопастей несущего винта вертолета Ми-34, изготовленных по намоточной технологии, составляет сегодня примерно $ 0,61. Даже если предположить, что в будущем она может снизиться почти вдвое и будет равна $ 0,36, то и тогда она в 10 раз превысит цену эксплуатации металлических лопастей.
Данные, приведенные в табл. 1, не учитывают изменяемость ресурсов и цен. Однако многолетние исследования показали, что конструктивные особенности лопастей вертолетов Ми-8, Ми-24 и Ми-2 позволяют эксплуатировать их «по состоянию». Достаточно установить действующую в полете систему сигнализации, и лопасти смогут эксплуатироваться в два раза дольше при весьма небольших затратах. В этом случае их конкурентоспособность в сравнении с композитными лопастями возрастет.
С учетом повышения наработок лопастей и в будущем ситуация не изменится. Как показано в табл. 2, композитные лопасти, изготовленные по намоточной технологии, проигрывают и в этом случае.
Не менее важным критерием оценки технологичности конструкции является процент брака при отладке технологии. В этом плане показателен опыт производства лопастей вертолета Ми-34, потому что разработчиком и производителем конструкции и технологии производства лопастей выступает МВЗ им. М.Л. Миля. За 20 лет произведено 120 лонжеронов лопастей. Из них забраковано или направлено на испытания (т.е. косвенно забраковано) 50 штук. Смена нескольких типов оснастки отбраковку практически не снизила. Величина ее составляет около 40 %.
Следующий показатель технологичности – сроки разработок и внедрения изделия в серийное производство. Имеет смысл отметить, что работы по созданию композитных лопастей начались более 25 лет назад практически одновременно на МВЗ им. М.Л. Миля и на УВЗ им. Н.И. Камова. Но камовские лопасти, изготовленные по укладочной технологии, уже давно имеют ресурс порядка 3000-4000 ч, в то время как ресурсы «милевских» лопастей несущего винта, созданных по технологии намотки, не превышают 600 ч.
Таблица 2
Вертолет Изготовитель Ресурс, который может быть установлен в ближайшее время, ч Стоимость 1 кг/ресурс $ США/R * 10-3 Ми-2 Польша 5000 17,5 Ми-8 Казань/Улан-Удэ 5000 16-20 Ми-26 Ростов-на-Дону 2500 38 Ми-24 Ростов-на-Дону 2500 48 Ми-34 Москва 1000 366Таблица 3
Вертолет Тип лопасти γ Относительный вес лопастей (к полетному весу) β Ми-2 металлические 4,04 4,45 х 10-2 12,0 Ми-8 металлические 6,5 5,87 х 10-2 11,60 Ми-26 металлические + композитные 7,0 -7,5 5,7 х 10-2 8,78 Ми-24 металлические 5,25 х 10-2 14,5 Ка-32 композитные,укладка ~ 4,36 3,8 х 10-2 15,0 Ми-34 композитные,намотка 3,9 4,3 х 10-2 19,0Влияние лопастей из композитов на конструкцию вертолета в целом
В табл. 3 приведены характеристики лопастей по параметру g, отражающему нагрузку на втулку и относительный вес лопастей.
Введем коэффициент р, который равен
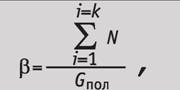
где k – число лопастей в несущем винте; N – центробежная сила лопастей; Спол – полетный вес.
Коэффициент р характеризует нагруженность втулки центробежными силами лопастей и косвенно оценивает отношение веса втулки к полетному весу.
Из табл. 3 следует, что нагруженность втулки несущего винта при использовании композитных лопастей больше, чем при использовании металлических лопастей традиционной конструкции. При этом лопасти, изготовленные по намоточной технологии, нагружают втулки в 1,1-1,65 раза больше, а лопасти, изготовленные по укладочной технологии, в 1,05-1,5 раза больше, чем металлические.
Подтверждение этому находим на рис. 1, где представлены обобщенные оценки весовых коэффициентов лопастей различных вертолетов. (См. Тищенко М.Н., Некрасов А.В., Радин А.С. «Вертолеты. Выбор параметров при проектировании», 1978 г.).
На этом же рисунке показаны весовые коэффициенты лопастей несущих винтов k*л с учетом различий в удлинениях лопастей (выделенная область относится к лучшим в весовом отношении конструкциям лопастей с дюралеалюминиевым прессованным лонжероном, стальным трубчатым лонжероном и стеклопластиковым каркасом; пунктирными линиями показаны границы минимально допустимого веса лопасти по условию g~7 (кл =5,5); приведены также кл рулевых винтов).
Весовой коэффициент лопастей Ми-34 в 1,15-1,2 раза выше коэффициента большинства традиционных лопастей. То, что эта величина сопоставима с величиной весового коэффициента лопастей вертолета Ка-26 (Ка-226), изготовленных по укладочной технологии, не может служить оправданием, так как эти лопасти были спроектированы около 30 лет назад. Более современные лопасти для вертолета Ка-32, изготовленные по укладочной технологии, имеют существенно меньший весовой коэффициент, равный 13,0, что подтверждает преимущество указанной технологии.
Итак, преимущество композитных лопастей, изготовленных по укладочной технологии, очевидно. Если судить по характеристикам лопастей вертолета Ка-32, укладочная технология позволяет снизить нагрузки на втулку на 10-15%, а также на 10-15 % уменьшить относительный вес лопасти в конструкции вертолета.
К тому же намоточная технология, обуславливая практически постоянные сечения лопасти по ее радиусу, не позволяет эффективно регулировать распределение материала как по сечению, так и по длине лопасти.
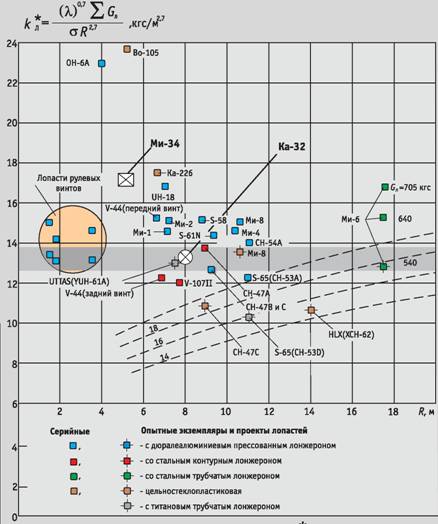
Рис. 1. Весовые коэффициенты лопастей несущих винтов k*л с учетом различий в удлинениях лопастей
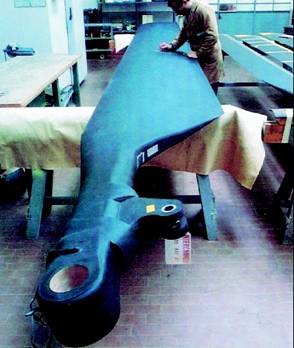
Лопасть вертолета CH-47
Перспективная оценка технологий
Прямоугольные в плане лопасти несущего винта были «навязаны» особенностями технологии изготовления лонжеронов металлических лопастей. Это, прежде всего, прессование в виде замкнутого полого профиля постоянного сечения по длине и требования необходимой усталостной прочности. Переход к серийному производству тоже привел к необходимости упрощения технологии, что сказалось прежде всего на выборе геометрии.
Если же говорить о весовом совершенстве вертолета и тяговых характеристиках несущего винта, более целесообразной является трапециевидная в плане лопасть, которая к тому же совсем необязательно должна иметь четко выделенную конструктивно-технологическую часть – лонжерон. Композиционные лопасти, изготовленные по укладочной технологии, легко переносят неизбежное увеличение переменных напряжений, возникающее в полете. Кроме того, технология укладки позволяет создавать лопасти различной геометрии, в том числе и трапециевидные, а также варьировать формы концевой ее части (законцовки).
Изготовление трапециевидных лопастей по укладочной методике технологических проблем не вызывает. При использовании же технологии намотки (если это вообще возможно) могут возникнуть большие сложности.
Стремление применять композиционные материалы при изготовлении лопастей вертолетов обусловлено необходимостью решения следующих задач:
- уменьшения веса лопастей и конструкции вертолета в целом и нагрузок на втулки;
- повышения усталостной прочности конструкции.
Однако нельзя сбрасывать со счетов и проблему экономической целесообразности данного решения.
Несомненно, что для боевых вертолетов, эксплуатирующихся в условиях больших скоростей и перегрузок, в будущем желателен переход на композиционные конструкции. Несомненно также, что использование композитов в конструкции средних и тяжелых вертолетов также может дать положительный эффект и выигрыш в весовом отношении.
Для небольших же вертолетов гражданского применения, скорости которых сравнительно невелики, нет необходимости применять композитные лопасти. Это экономически нецелесообразно.
Не исключено, что какую-то нишу могут занять слоистые конструкции из листовых материалов. Возможно, это позволит создать менее дорогие лопасти с большими ресурсом и надежностью. Разумеется, последнее положение требует серьезной конструкторской и технологической проработки.
В заключение можно уверенно сказать, что композитные лопасти лонжеронной конструкции, спроектированные под намоточную технологию, не имеют преимуществ по ресурсам и значительно дороже лопастей, изготавливаемых по укладочной технологии. Кроме того, требуется значительно больше усилий и времени для их внедрения, что ставит под сомнение целесообразность применения данной технологии.
Зиновий ШНУРОВ, начальник отдела МВЗ им. М. Л. Миля, канд. техн. наук, лауреат Государственной премии
ТЕХНОЛОГИЯ
Более 800 000 книг и аудиокниг! 📚
Получи 2 месяца Литрес Подписки в подарок и наслаждайся неограниченным чтением
ПОЛУЧИТЬ ПОДАРОК