Хроники первых «тридцатьчетверок» 1940 г Начало пути
Хроники первых «тридцатьчетверок» 1940 г
Начало пути
Алексей Макаров
Продолжение. Начало см. в «ТиВ» № 9-12/2010 г. № 1–5/2011 г.
27 апреля 1940 г. членами комиссии был подписан отчет по итогам проведенных войсковых испытаний двух опытных Т-34, а также составлен перечень изменений и доработок, подлежащих обязательному внесению в конструкцию серийных танков. После всестороннего изучения данного отчета начальник АБТУ КАД.Г. Павлов отправил на имя народного комиссара обороны С.К. Тимошенко доклад следующего содержания:
20 мая 1940 г. № 73034с
НАРОДНОМУ КОМИССАРУ ОБОРОНЫ СОЮЗА СССР МАРШАЛУ СОВЕТСКОГО СОЮЗА тов. ТИМОШЕНКО
Представляю на утверждение отчет комиссии по войсковым испытаниям опытных образцов танка Т-34, принятого на вооружение Красной Армии Постановлением Комитета Обороны при СНК Союза ССР№ 44Зссот 19 декабря 1939 года.
По вопросам, выдвинутым в особых мнениях (стр. 83–85 отчета) представителем АУ КА. Военинженером 2 ранга т. СОРКИНЫМ и завода № 183 тов. МОРОЗОВЫМ, докладываю:
1. Расширение башни на 160 мм, без переделки погона башни и корпуса, предложенное заводом № 183 мною утверждено. С увеличением высоты башни не согласен, т. к. это ведет к увеличению цели для противника, а надобности в этом нет, ибо угол склонения -5° вперед и по бортам обеспечен.
2. С унификацией качающихся частей орудия с танками другого класса не согласен, т. к. это приведет к увеличению веса танка Т-34.
3. По работе главного фрикциона, разногласий по существу нет, т. к. завод сам признал, что причины коробления дисков установить еще не удалось. Коробление же дисков является существенным дефектом.
4. Ленивец мною утвержден по второму варианту, с внутренним регулированием натяжения гусеницы, как наиболее прочный и защищенный от поражений.
5. Установку рации настаиваю перенести в носовую часть танка, дабы освободить командира танка для ведения боя. В носовой части танка предусмотрено место радиста-стрелка.
6. Конструкцию смотровых приборов настаиваю переделать за счет применения металлических зеркал и триплекса.
7. Прибор кругового обзора на 1940 год утвердил в том виде, как он представлен на опытных образцах.
В первых числах июня с/г завод № 183 изготовит опытную партию (10 шт.) танков Т-34 по чертежам опытного образца.
Мною дано разрешение заводам Мариупольскому (по броне) и № 183 на изготовление еще 10 танков Т-34 по чертежам опытного образца, дабы тщательней отработать технологию производства к серийному выпуску.
Отчет Комиссии по войсковым испытаниям и мои решения прошу утвердить.
ПРИЛОЖЕНИЕ: Упомянутое на 85 листах.
НАЧАЛЬНИК АБТУ КРАСНОЙ АРМИИ КОМАНДАРМ 2 РАНГА ПАВЛОВ ВОЕННЫЙ КОМИССАР АБТУ КР. АРМИИ ДИВИЗИОННЫЙ КОМИССАР КУЛИКОВ. [1]
Отчет по войсковым испытаниям с перечнем доработок, а также решения, принятые Д.Г. Павловым по конструкции машины, были утверждены наркомом обороны С.К. Тимошенко 31 мая 1940 г. Таким образом, дальнейшие работы по подготовке серийного производства танка Т-34 официально получили зеленый свет на самом высоком уровне.
Теперь рассмотрим ситуацию, сложившуюся с разработкой и производством бронедеталей для танка Т-34. На протяжении мая- июня конструкторы завода № 183 совместно со специалистами Мариупольского завода активно занимались созданием, уточнением и согласованием чертежей на бронедеталитанкаТ-34для их серийного производства в 1940 г. В начале мая КБ 520, во исполнение ранее предъявленных НКО требований о расширении башни, разработало проект и подготовило комплект чертежей на новую башню Т-34. Увеличение внутреннего объема башни в зоне расположения экипажа было достигнуто за счет смещения линии сгиба боковых стенок башни (детали 34.30.018-1 и 34.30.019-1) от центра башни в сторону кормы на 162 мм. Эта мера позволила оставить диаметр погона и углы наклона брони башни прежними, но из-за изменения ее общей геометрии основные бронедетали претерпели существенные изменения. Такое конструктивное решение по расширению башни, как показало будущее, практически не улучшило условий работы экипажа, но, тем не менее, проект был одобрен Д.Г. Павловым.
Необходимо заметить, что более радикальное расширение башни путем увеличения диаметра погона повлекло бы за собой неизбежные изменения в конструкции корпуса, а также ряда узлов и агрегатов танка, на разработку которых ушло бы неопределенное время. На тот момент это было недопустимо, так как новые танки требовались армии в кратчайшие сроки.
Однако, несмотря на то, что данный проект башни получил одобрение на столь высоком уровне, в серийное производство в первоначальном виде его не приняли. Дело в том, что 21 мая 1940 г. на Мариупольском заводе состоялось техническое совещание, темой которого стало рассмотрение и согласование измененных чертежей танка Т-34. На этом совещании рассматривались и новые детали расширенной башни. Ниже приведем выписки из протокола совещания:
По детали 34-29-019 (бронировка курсового пулемета. — Прим. авт.) — литая, ОГТ разработать чертеж для литья, срок 28/V.
По детали 34-15-006 (крышка ленивца) — поставляется без зашлифовки внешней конфигурации после огнереза. Увеличить радиусы закругления у выступов для болтов до 50 мм. Деталь изготовляется из заготовки 25 мм. Утонение допускается до 19,5мм.
По деталям 34-12-013 (крышка поддерживающего колеса) и 34-15-006 — Конструкторам завода № 183 проработать чертежи с расчетом производить штамповку одним штампом.
По детали 34-16-003 (крышка бортовой передачи) — крышка литая, Мариупольский завод к изготовлению не принимает.
По деталям 34-30-018-1 и 34-30-019-1 (боковые стенки башни) по предложенным чертежам не могут быть приняты к изготовлению ввиду отсутствия на заводе соответствующего оборудования по штамповке, а также правильных средств после закалки.
По детали 34-29-877-1 (перемычка над люком водителя) — Старшему конструктору завода № 183 совместно с Зам. начальника цеха № 5 тов. ЗАСЕДСКИМ с целью облегчения обработки, проработать изменения впадины для петли.
ОСОБОЕ МНЕНИЕ ПРЕДСТАВИТЕЛЕЙ ЗАВОДА № 183 И ВОЕНПРЦДА АБТУ КА НА ЗАВОДЕ № 183
3. По детали 34-16-003 отказ Марзавода от поставки сырых заготовок этих деталей по мотивам отсутствия литейной базы для отливки этих деталей, не может быть принят заводом № 183, т. к. по другим узлам машины Марзавод предлагает замену катаных и штампованных узлов — литыми или же комбинированными, в которые входят литые элементы. Для отливки этих элементов литейная база на заводе Ильича имеется, следовательно, отливку двух деталей меньших, как по весу, так и по габаритам, завод Ильича имеет полную возможность выполнить.
4. По деталям 34-30-018-1 и 34-30-019-1 эти детали требуют изготовления новых штампов, несколько отличающихся от аналогичных штампов, запроектированных для изготовления детали 34-30-018и 34-30-019. Никакого дополнительного оборудования по штамповке и правильных средств изменение этих деталей не требует, и всю последующую обработку после штамповки можно вести по техпроцессу на детали 34-30-018 и 34-30-019.
Данные изменения в деталях 34-30-018 и 34-30-019 сделаны с целью уширения колпака по указанию НКО, которые согласовывались с Зам. начальника 5 цеха з-да Ильича т. ЗАСЕДСКИМ во время изготовления чертежей на заводе № 183. Отказ от изготовления колпака заводом Ильича даже без тщательной проверки конструкции и возможности его изготовления, является формальной необоснованной отпиской, которая может привести к срыву выпуска машин А-34.
ПРЕДСТАВИТЕЛИ ЗАВОДА 183Таршинов
Кочетов
Щербаков
ВОЕНПРЩ АБТУ КА ПРИ ЗАВОДЕ 183 Русаков. [2]
Таким образом, несмотря на мнение представителей завода № 183 и АБТУ, Мариупольский завод отказался принять к изготовлению новые боковые листы башни, ссылаясь на сложность их конструкции и отсутствие необходимого оборудования. Чуть позднее директор и главный инженер Мариупольского завода отправили в адрес руководства завода № 183, АБТУ и 7-го ГУ НКСП письмо, объясняющее позицию завода:
28/V 1940 г.
№ 2757
К протоколу совещания от 21А/-40 г.
Настоящим сообщаем, что завод № 183 не выполнил указаний АБТУ КА в части упрощения деталей машины А-34, в частности детали 34-30-018-1 и 34-30-019-1 по предложенным чертежам еще более усложнились.
Для установочной партии детали полубашни штамповались на прессе цеха № 5 с четырех операций, такая штамповка была весьма сложной, т. к. требовала после каждой операции самостоятельной разметки. По новым чертежам детали полубашни (34-30-018-1 и 34-30-019-1) имеют отбуртовку, которую нельзя получить на существующих прессах цеха № 5 ввиду их малой мощности (450 тонн).
Мариупольский завод в период производства установочной партии пробовал производить штамповку детали полубашни на прессе 3000 тонн цеха № 8, но ввиду того, что пресс имеет подвижной стол, на котором матрица в период штамповки смещается относительно оси пуансона, эти детали не удалось получить даже приближенных размеров. Детали полубашни с отбуртовкой еще больше усугубят невозможность их получения, т. к. даже путем получения кустарным способом, при больших затратах, деталей с отбуртовкой, последние в процессе закалки будут иметь неизбежную поводку, неустранимую правильными средствами (вальцами) существующим на заводе оборудованием.
Исходя из вышеизложенного, Мариупольский завод отказывается от принятия изготовления этих деталей и просит завод № 183 дополнительно проработать вопрос упрощения этих деталей с целью обеспечения выпуска машины А-34 в требуемом количестве.
ДИРЕКТОР ЗАВОДА /ГАРМАШЕВ А.Ф./ ГЛАВНЫЙ ИНЖЕНЕР/НИЦЕНКО/[3]
Таблица № 7
Наименование детали «Узкая» башня (сборочный чертеж 34.30 сб), изготовлено 37 комплектов Первый вариант расширенной башни (в серию не пошел) Первый серийный вариант расширенной башни (сборочный чертеж 34.30 сб-1) Лобовой лист башни 34.30.001 34.30.001 34.30.001 Передняя обечайка башни 34.30.006 34.30.006-1 34.30.006-1 Задняя обечайка башни 34.30.007 34.30.007-1 34.30.007-2 Передний лист крыши башни 34.30.008 34.30.008-1 34.30.008-1 Днище ниши башни 34.30.009 34.30.009-1 34.30.009-2 Крышка люка башни 34.30.010 34.30.010-1 34.30.010-1 Дверка ниши башни 34.30.011 34.30.011-1 34.30.011-2 Задний лист крыши башни 34.30.017 34.30.017-1 34.30.017-1 Правый лист башни 34.30.018 34.30.018-1 34.30.018-2 Правый лист башни 34.30.019 34.30.019-1 34.30.019-2 Основания смотрового прибора 34.30.051 (2 шт.) 34.30.183; 34.30.184 34.30.183; 34.30.184В результате, КБ завода № 183 было вынуждено изменить конструкцию башни, сделав ее более технологичной и приемлемой для изготовления на Мариупольском заводе. Новый вариант расширенной башни был разработан к началу июня 1940 г. (получивший впоследствии индекс 34.30сб-1) и отличался от первоначального варианта, не принятого в производство, в основном конструкцией боковых листов — деталей 34.30.018-2 и 34.30.019-2. Увеличение внутреннего объема башни в зоне расположения экипажа и способ его достижения (смещение линии сгиба боковых листов от центра башни в сторону кормы на 162 мм) остались прежними. При этом по сравнению с первоначальным вариантом не претерпел изменений ряд деталей башни — лобовой лист, листы крыши, крышка люка и др. (см. таблицу № 7).
Параллельно с согласованием чертежей для серийного производства в мае 1940 г. на Мариупольском заводе активно велись опытные работы по упрощению технологии изготовления бронедеталей. Еще в середине апреля 1940 г. главный технолог Мариупольского завода им. Ильича Д.И. Чижиков в инициативном порядке обратился к руководству АБТУ и НКСП с письмом, в котором предложил при изготовлении наиболее трудоемких и крупных деталей танка Т-34 использовать вместо остродефицитного 3000-тонного пресса имеющийся на заводе новый 15000-тонный ковочный пресс. Такая мера позволила бы существенно разгрузить имеющееся на заводе оборудование. Кроме этого, Д.И. Чижиков выступил с инициативой кардинально изменить броневую защиту танка Т-34, заменив сварные конструкции цельноштампованными узлами, придав таким образом корпусу обтекаемую форму, что, по мнению главного технолога, привело бы к удешевлению производства и повышению бронестойкости танка. Ниже приведем выписки из этого письма:
В целях: а) ликвидации на заводе узкого места по штамповке крупных и наиболее сложных бронедетапей корпуса танка А-34, б) организации массового и бесперебойного выпуска деталей этой машины, в) полного освобождения от штамповки деталей А-34 3000-тонного правильного пресса, неприспособленного для этой работы и сильно загруженного производством корабельной брони и г) создания совершенно новой по конструкции броневой защиты танка А-34 путем применения цельноштампованных узлов, что даст возможность получить обтекаемость корпуса и башни и повышение бронестойкости, ПРЕДЛАГАЮ ИСПОЛЬЗОВАТЬ ИМЕЮЩИЙСЯ НА ЗАВОДЕ ИМ. ИЛЬИЧА 15000 тонный КОВОЧНЫЙ ПРЕСС.
Параметры, мощность и вспомогательное оборудование пресса вполне позволяют выполнить штамповку, как отдельных деталей по существующим чертежам, так и осуществить штамповку целых узлов корпуса танка.
Использование 15000 тн. пресса для указанной цели почти не отразится на выполнении прессом его основной программы — ковке слитков на слябы для корабельной брони, т. к. штамповка деталей или узлов машины А-34 может быть выполнена в паузах между нагревами слитков.
Штамповка деталей на 15000 тонн, прессе по существующим чертежам может быть осуществлена немедленно в имеющихся штампах с небольшими их переделками, необходимыми для крепления в условиях 15000 тонн, пресса. Для штамповки узлов необходимо произвести переконструирование всей броневой защиты танка А-34. Проектирование цельноштампованных узлов следует выполнить силами конструкторов завода № 183 (3 человека) и работниками нашего завода. При такой организации работы в кратчайший срок будет решен вопрос, как рациональной формой броневой защиты, так и технологии штамповки.
ГЛАВНЫЙ ТЕХНОЛОГ ЗАВОДА ИМ. ИЛЬИЧА Д. И. ЧИЖИ КОВ. [4]
Данное предложение заинтересовало руководство АБТУ и НКСП, и 22 апреля 1940 г. заместитель председателя Госплана СССР М.З. Сабуров направил на имя директора и главного технолога Мариупольского завода письмо с предложением разъяснить некоторые технические моменты и представить расчеты по количеству времени, необходимого для изготовления одной детали:
На Ваше письмо от 15. IV-1940 г. № 1935 об использовании пресса 15 т. тонн давления для штамповки (гибки) деталей к танку А-34 в паузах между нагревами слитков, прошу сообщить следующие данные:
1. Как велики по продолжительности эти паузы с учетом, что существующие проектируемые нагревательные печи должны обеспечить нагрев и подогрев слитков для непрерывной работы пресса.
2. Если после этого действительно окажутся паузы, то сколько потребуется времени на переналадку пресса с ковки на штамповку (гибку).
3. Учитываете ли Вы, что пресс 15 т. тонн кроме обжатия слитков в слябидля брони будет ковать др. заготовки (валы прокатные и др., барабаны и т. п.).
4. Поскольку штамповка деталей к танку А-34 должна производиться с нагревом — сколько печечасов на это дело уйдет на один комплект.
Что Вы можете сказать после учета моих замечаний?
Сообщите потребное время в прессочасах на 1 шт. с учетом наладок и переналадок пресса.
ЗАМ. ПРЕДСЕДАТЕЛЯ ГОСПЛАНА ПРИ СНК СССР М.З. Сабуров. [5]
Чертеж переднего листа крыши (деталь 34.30.008-1) первого серийного варианта расширенной башни Т-34.
Эскиз цельноштампованной носовой детали, разработанный по предложению Д.И. Чижикова.
После получения необходимых разъяснений Мариупольскому заводу было предписано провести опытные работы по изысканию возможности штамповки крупных деталей Т-34 на 15000-тонном прессе, а также изготовлению цельноштампованного носа конструкции, предложенной Д.И. Чижиковым.
Но основные работы по упрощению технологии изготовления сложных бронедеталей танка Т-34 в мае-июне 1940 г. велись в направлении проектирования и изготовления опытных литых узлов корпуса и башни. Как уже было сказано, начиная с апреля 1940 г., сотрудники бригады по литым узлам изучали возможность изготовления разрезной комбинированной носовой части корпуса Т-34 вместо цельноштампованного носа, утвержденного на установочную серию. Вариант комбинированного носового узла был спроектирован в середине апреля 1940 г. силами КБ 520 завода № 183 и представлял собой конструкцию, состоявшую из трех деталей: две из них являлись прямолинейными катаными листами высокой твердости, а одна деталь (балка) — литой, имевшей V-образное сечение с углом раствора 60”.
При выборе марки стали и типа брони для балки учитывалось, во-первых, ее максимальная толщина (100 мм) и, во-вторых, необходимость получения после окончательной термической обработки литой детали в состоянии, допускающем ее механическую обработку после высокого отпуска. Как наиболее приемлемую по своим литейным и броневым качествам для литой балки низкой твердости наметили сталь марки ФД-6654 с небольшой добавкой ванадия. Эта марка стали обеспечивала на данной толщине достаточную прокаливаемость и необходимые физико-механические свойства после закалки и высокого отпуска.
Кроме ФД-6654, большой практический интерес и значительные производственные удобства представляло использование для изготовления литой балки, идущей на валовом производстве, стали марки МЗ-2. Но применение МЗ-2 требовало предварительного исследования, поскольку на больших толщинах (более чем 55–60 мм) она до этого не производилась. Для исследования прокаливаемости и качества излома литой брони марки МЗ-2 на больших толщинах специалисты бригады вырезали из прибылей литой башни пробы размером 200x150x300, которые были закалены в различных средах и отпущены на температуру 680”. В дальнейшем анализ вида изломов и твердости по сечению термически обработанных проб показал полную возможность применения стали МЗ-2 для изготовления литых конструкций больших толщин. Таким образом, для изготовления опытных литых носовых балок были намечены две марки стали: ФД-6654 и МЗ-2.
Первые опытные литые балки были изготовлены по следующей технологии.
Формовка производилась горизонтально, по чистым моделям, в двух спаренных между собой опоках. В каждой опоке осуществлялась формовка одновременно трех деталей. Состав формовочной земли: часовъярский песок (жирный) — 35 %, еленовский песок (кварцевый) — 50 %, маршалит — 15 %.
Литниковая система была выполнена в шамотных трубках: стояк диаметром 70 мм, горизонтальный литниковый ход диаметром 55 мм, питатели диаметром 40 мм. Металл подводился сифоном в нижнюю торцевую часть детали. Окраска формы производилась маршалитовой краской на паточном растворе. Сушили форму в течение 8-10 ч при температуре 300–350°. Заливка форм жидким металлом производилась вертикально, из ковша с диаметром стаканчика 45 мм. Прибыля до 1/3 высоты заполнялись сифоном, после чего происходила доливка прибылей сверху, непосредственно в прибыля, с последующей засыпкой их термитом. Затем детали выдерживались в земле в течение 40 ч. В таблице № 8 приведен химический анализ опытных литых балок.
В дальнейшем все опытные литые балки подвергли отпуску на температуру 680”, после чего от них удалили прибыля. Термическая обработка литых балок проводилась по нескольким режимам.
Балки, отлитые из стали ФД-6654, в количестве 3 штук и балки из стали МЗ-2 обрабатывались по режиму:
1. Первая закалка: 920–930° -4 ч, охлаждение в масле;
2. Высокий отпуск: 670–680° -7 ч, охлаждение в воде;
3. Вторая закалка: 870–880° -4 ч, охлаждение в масле;
4. Высокий отпуск: 670–680° — 7 ч, охлаждение в воде;
5. Окончательная закалка: 830–840° -5 ч, охлаждение в масле;
6. Окончательный отпуск различный:
а) для деталей марки ФД-6654 — отпуск при температуре 600–610° — 10 ч, охлаждение в воде;
б) для деталей марки МЗ-2 — отпуск при температуре 620–625° -12 ч, охлаждение в воде.
Остальные три балки из стали ФД-6654 обрабатывались с предварительной гомогенизацией по режиму:
1. Гомогенизация:
а) посадка при 650–680° и последующий нагрев до 1050–1100° со скоростью 70–80° в час;
б) выдержка при 1050–1100° — 8 ч;
в) охлаждение детали на воздухе до 450”;
г) выдержка при 450° — 2 ч;
д) подъем до 650–680° и выдержка 10 ч;
е) выдача деталей на воздух;
2. Закалка: 870° -4 ч, охлаждение в масле;
3. Высокий отпуск: 670–680° — 7 ч, охлаждение в воде;
4. Окончательная закалка: 830–840° -5 ч, охлаждение в масле;
5. Окончательный отпуск: 600–610° — 10 ч, охлаждение в воде.
Таблица № 8
Марка стали Способ выплавки Химический анализ в %% Кол-во деталей C Si Mn S P Cr Ni Mo V МЗ-2 Дуплекс процесс, мартеновская печь 0,23 1,32 1,38 0,013 0,018 0.92 1.41 0,17 - 3 ФД-6654 Основная электро-печь 0,38 0.42 0,44 0,013 0,013 1,56 2,39 0,42 0.15 6
Чертеж крышки башенного люка (деталь 34.30.010-1) первого серийного варианта расширенной башни Т-34.
Копия чертежа опытного комбинированного носового узла. Чертеж подписан старшим конструктором завода № 183 М.И. Таршиновым 15 апреля 1940 г.
После окончательной термической обработки было взято по одной детали каждого варианта, которые после надреза огнем поломали под прессом для получения данных по виду излома, качеству отливки и твердости по сечению. Наилучший излом показала литая балка из стали МЗ-2. Худшие изломы наблюдались у балок, изготовленных из стали ФД-6654, — в них были обнаружены значительные участки столбчатых кристаллов. При этом кристаллические зоны наблюдались как у балок из стали ФД-6654, прошедших гомогенизацию, так и термически обработанных без нее.
В отношении качества отливки на всех трех изломах в центральной части наблюдались чистые, не загрязненные посторонними включениями, усадочные раковины или усадочная рыхлость. Это указывало на недостаточное питание центра отливки жидким металлом в процессе ее затвердевания. В дальнейшем путем некоторого изменения технологии специалистам бригады удалось увеличить плотность отливки в центральной части балки, таким образом, повысив качество детали. Твердость опытных литых балок, замеренная по сечению, в зоне плотного металла оказалась равномерной и лежала в пределах 3,6–3,7 для деталей из стали ФД-6654 и 3,8–3,9 — для деталей из стали МЗ-2.
Несмотря на обнаруженные в центральной части отливок рыхлости, балки по качеству волокна и твердое™ были признаны годными и отправлены на механическую обработку, включавшую в себя строжку кромок, изготовление фаски для сварного шва, сверловку отверстий и нарезку резьбы для гужонного соединения. Затем на Мариупольском заводе собрали два макета носового узла: один из стали марки ФД-6654 (без гомогенизации), второй из стали МЗ-2; сварка производилась электродами «МД». После сборки носовой узел из стали МЗ-2 (для снятия закалочных напряжений в зоне сварного шва) был подвергнут низкому отпуску на температуру 270° и направлен на испытания.
Первые полигонные испытания опытного носового узла с литой балкой состоялись в периоде 16 по 20 мая 1940 г. на полигоне Мариупольского завода им. Ильича. На испытаниях присутствовали: старший военпред АБТУ на заводе им. Ильича Г.И. Зухер, заместитель начальника исследовательской лаборатории Г.И. Капырин, заместитель начальника цеха № 5 Г.Ф. Заседский, начальник 6 отдела НИИ-48 М.Я. Герасимов и старший инженер 2 отдела НИИ-48 Б.К. Василевский.
Комиссии предстояло оценить бронестойкостъ литой балки и мест гужонных и сварных соединений при обстреле снарядами калибра 37 и 45 мм, а также проверить характер поражений всего узла при попадании 76-мм бронебойного снаряда.
РЕЗУЛЬТАТЫ ПОЛИГОННЫХ ИСПЫТАНИЙ КОМБИНИРОВАННОГО НОСОВОГО УЗЛА.
По 37 мм бронебойному снаряду.
Испытания носового узла производилось 37 мм бронебойными снарядами чертеж 3882 под углом 0° и в рабочем положении носовой детали (угол 60°).
В результате испытаний носового узла, главным образом в местах стыка литой детали с катаной, было найдено, что только при обстреле по нормали, с максимальной скоростью, 37 мм бронебойный снаряд в этих местах узла может вызвать нарушение тыльной прочности и небольшие местные разрушения сварного шва. Под углом обстрела 60°, бронебойный снаряд 37мм калибра или рикошетирует, или в лучшем случае производит небольшие выбоины на лицевой стороне, без каких-либо следов с тыльной поверхности.
По 45 мм бронебойному снаряду.
Обстрел носового узла 45 мм бронебойным снарядом производился как в рабочем положении (угол 60°), так и под углами 30° и 0°. Испытание во всех случаях производилось со штатными скоростями (750–770 м/с).
При испытании по нормали, в местах попадания снаряда между гужонами наблюдались подрывы пробки и небольшие разрушения сварного шва в виде трещин.
При испытании под углом 30°, во всех случаях не наблюдалось нарушения тыльной прочности узла, за исключением местных трещин сварного шва в месте поражения.
При испытании под углом 60° -45 мм снаряд, как и снаряд 37 мм калибра, или рикошетирует, или производит небольшие разрушения на лицевой стороне, без каких-либо последствий для тыльной стороны.
По 76 мм бронебойному снаряду.
Испытания 76 мм бронебойным снарядом преследовало главным образом проверку прочности гужонных и сварных соединений всего комбинированного узла в целом. Несмотря на жесткость испытаний (испытание 76 мм снарядом производилось последним, после испытания носового узла снарядами 37 и 45 мм калибров) носовой узел показал вполне удовлетворительные результаты.
При скорости снаряда 569 м/с в носовую деталь (под углом близким к нормали) последняя дала небольшую выбоину без выпучины с тыла и относительно небольшую трещину сварного шва. Второй снаряд при скорости 620 м/с под углом 60° (по месту сварки) срикошетировал и вызвал в катаной 45 мм детали высокой твердости откол около 180 мм в диаметре, т. е. менее 3-х калибров. [6]
Данные по срабатываемости бронебойных снарядов также оказались удовлетворительными: корпуса 37- и 45-мм снарядов во всех случаях были либо со вскрытыми полостями, либо в осколках. На основании полученных результатов комиссия сделала следующие выводы:
Общее заключение о стойкости комбинированного носового узла.
Комбинированный носовой узел в рабочем положении и под углом 30° надежно выдерживает — без нарушения прочности — удар 37 и 45 мм бронебойных снарядов при максимальных скоростях.
При обстреле под углом 0° комбинированный носовой узел поражается этими снарядами при штатных скоростях последних только в зоне гужонных и сварных соединений. Причем характер наблюдаемых поражений узла при этом — надрыв пробки не на полную окружность, трещины на выпучине — нужно охарактеризовать как безопасные поражения.
Учитывая, что в действительных условиях службы комбинированного носового узла на машине попадания в зону гуженных и сварных соединений по нормали маловероятны (возможны при подъеме или спуске танка под углом 60°) следует признать, что практически, при иных углах подъема танка, комбинированный носовой узел практически не будет поражаться бронебойными снарядами 37 и 45 мм калибров даже при стрельбе в упор. В отношении 76 мм бронебойного снаряда, испытания которым проводились факультативно, стойкость и характер поражения литой носовой детали следует считать удовлетворительной.
Надежность гужонных и сварных соединений узла.
Снарядные испытания комбинированного носового узла, в основном сводящиеся к испытанию гужонных и сварных соединений снарядами различных калибров и под разными углами показали удовлетворительные результаты. Носовой узел выдержал 24 выстрела, без значительных повреждений в местах гужонных и сварных соединений.
ВЫВОДЫ
На основании результатов испытания комбинированного носового узла машины А-34, изготовленного из стали марки И-8С (МЗ-2) следует заключить:
1) По стойкости против 37 и 45 мм бронебойных снарядов, комбинированный носовой узел не пробивается (в рабочем положении) снарядами этих калибров, при максимальных скоростях последних.
2) При испытании бронебойным снарядом 76 мм калибра литая носовая деталь в высокоотпущенном состоянии показала удовлетворительные результаты, как по стойкости против этого калибра, так и по характеру поражений.
3) Гужонные и сварные соединения катаных деталей слитой — по результатам снарядных испытаний также вполне удовлетворительны. Во всех случаях попадания снаряда в гужоны или место сварки не вызывали каких-либо разрушений, выходящих за зону деформации.
4) Срабатываемость корпусов бронебойных снарядов 37 и 45 мм калибров удовлетворительная.
5) Применение комбинированного носового узла для машины А-34 взамен штампованного в значительной степени разгружает прессовое хозяйство завода, не снижая стойкости узла.
ЗАКЛЮЧЕНИЕ
В целях быстрейшей реализации в производстве комбинированного носового узла, взамен принятого в настоящее время штампованного, считать целесообразным:
1) Изготовить установочную партию в 10–15 шт. комбинированных узлов и установить их на корпуса.
2) Провести параллельные снарядные испытания штампованного и комбинированного узлов, в целях сравнения их стойкости.
3) При подтверждении положительных результатов перевести производство штампованной носовой детали машины А-34 целиком на комбинированный носовой узел. [7]
Не дожидаясь официального завершения полигонных испытаний комбинированного носового узла, 19 мая 1940 г. главный инженер Мариупольского завода B.C. Ниценко направил в АБТУ КА и 7 ГУ НКСП телеграмму следующего содержания:
СЕРИЯ Г ДВА АДРЕСА МОСКВА АБТУ КА АЛЫМОВУ КОПИЯ БАРЬЕР ЕМЕЛЬЯНОВУ-
РЕЗУЛЬТАТЫ ИСПЫТАНИЙ СВАРОЧНОГО НОСА ЛИТОЙ ВСТАВКОЙ ПРОТИВ 45 ХОРОШИЕ ЗПТ ПОДТВЕРДИТЕ ЗАПУСК ПРОИЗВОДСТВО ТЧК ПОДРОБНЫЕ МАТЕРИАЛЫ ПОЧТОЙ-
02/2223 НИЦЕНКО ФЕДОРОВ РУСАКОВ. [8]
В конце мая, после изучения полученных отчетов по испытанию комбинированного носового узла, АБТУ и НКСП разрешило Мариупольскому заводу изготовление установочной серии литых балок из стали марки МЗ-2, о чем уведомило завод телеграммой.
4 июня 1940 г. в АБТУ КА состоялось совещание под председательством помощника АБТУ Б.М. Коробкова, посвященное выполнению увеличенного годового задания по выпуску бронедеталей для Т-34 и выбору оптимальных путей для проведения опытных работ по упрощению конструкции наиболее трудоемких деталей. На совещании присутствовали: начальник и главный инженер 7-го ГУ НКСП B.C. Емельянов и А.А. Хабапашев, директор Мариупольского завода А.Ф. Гармашев, старший военпред Г.И. Зухер, а также начальники 8 отдела АБТУ С.А. Афонин и 4 отдела АБТУ Н.Н. Алымов. В ходе совещания сторонами были приняты следующие решения:
1. Работу по обеспечению выпуска корпусов танка Т-34 вести одновременно в нескольких направлениях — литье и штамповка.
2. Мариупольский завод немедленно приступает к освоению штампованных бронедеталей на 15000-тонном прессе (по предложению главного технолога Чижикова Д.И.) и к освоению изготовления башен и кормы Т-34 методом литья.
Излом опытной литой носовой балки из стали ФД-6654 после окончательной термообработки без гомогенизации (слева) и с гомогенизацией.
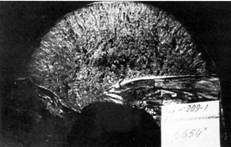
3. Основной упор в опытных работах сделать на освоении изготовления литых бронедеталей. По итогам совещания, 5 июня 1940 г. АБТУ и НКСП издали совместное распоряжение о форсировании работ по изготовлению литых узлов для танка Т-34.
№ 2231с
ДИРЕКТОРУ МАРИУПОЛЬСКОГО ЗАВОДА т. ГАРМАШЕВУ ДИРЕКТОРУ ЗАВОДА № 183 т. МАКСАРЕВУ СТ. ВОЕНПРЕДУ АБТУ КА НА МАРИУПОЛЬСКОМ ЗАВОДЕ т. ЗУХЕРУ СТ. ВОЕНПРЕДУ АБТУ КА НА ЗАВОДЕ № 183 т. КОЗЫРЕВУ КОПИЯ: И.О. ДИРЕКТОРА НИИ-48 тов. КОНЕВСКОМУ
С целью быстрейшего внедрения в производство литых деталей для машины «А-34» предлагается:
1. Мариупольскому заводу дополнительно к 10 литым вставкам носовой детали А-34, изготовление которых разрешено телеграммой АБТУ КА и 7 Главного Управления НКСП, изготовить еще 1 литую вставку, собрать носовой узел и провести контрольный отстрел его.
При получении на этом носовом узле стойкости, равной стойкости катаной 45 мм брони под теми же углами, носовые узлы с литой вставкой окончательно принимаются на валовое производство.
2. Мариупольскому заводу к 20. VI изготовить по чертежам завода № 1835 литых башен А-34, обеспечивающих бронестойкость равную бронестойкости башни из 45 мм катанной брони при превышении веса не более чем на 200 кг по сравнению с башней из катанной брони, включая вес крепежа. Одну башню направить на полигонные испытания, а четыре сдать заводу № 183 для монтажа на серийных машинах, при получении положительных результатов.
3. Заводу № 183 сдать Мариупольскому заводу чертежи литой башни с уширением не позднее 10. VI-1940 г.
4. Мариупольскому заводу на основе испытаний опытных литых деталей дать не позднее 20. VI совместное с заводом № 183 заключение о возможности принятия на валовое производство литой кормы А-34.
НАЧАЛЬНИК АБТУ КР. АРМИИ КОМАНДАРМ 2 РАНГА (ПАВЛОВ) ВОЕННЫЙ КОМИСАРАБТУКР. АРМИИ ДИВИЗИОННЫЙ КОМИССАР (КУЛИКОВ) НАЧАЛЬНИК 7-го ГЛАВНОГО УПРАВЛЕНИЯ НКСП (ЕМЕЛЬЯНОВ). [9]
Кроме этого, начальник 7-го ГУ НКСП B.C. Емельянов обязал дирекцию Мариупольского завода ускорить проведение опытных работ по изготовлению цельноштампованного носового узла корпуса Т-34, предложенного Д.И. Чижиковым:
№ 2228с от 05.06.40 г.
ДИРЕКТОРУ МАРИУПОЛЬСКОГО ЗАВОДА тов. ГАРМАШЕВУ Копия: НАЧАЛЬНИКУ АБТУ КА КОМАНДАРМУ 2-го РАНГА тов. ПАВЛОВУ
В целях быстрейшего проведения опытной работы по изготовлению цельно-штампованного носа Т-34 на 15000тн. ковочном прессе и создания этим дополнительного резерва в мощностях, предлагаю в пятидневный срок выслать в Главк и АБТУ план работ, намеченных заводом в этом направлении, с указанием сроков исполнения, как отдельных этапов, так и работы в целом. К плану намеченных работ обязательно приложить эскиз цельно-штампованного носа, намеченного к изготовлению на 15000 тн. прессе, увязав предварительно конструкцию его с конструкторами завода № 183, находящимися на заводе им. ИЛЬИЧА.
Кроме этого дать: а) потребные размеры бронелистов; б) технологию правки термически обработанной детали; в) намечаемую технологию механической обработки цельно-штампованного носа с указанием станочного оборудования для этих целей.
Этот расчет дать в сравнении с технологией изготовления как штампованного носа, изготовленного по технологии принятой на первых 10-ти комплектах машин, так и в сравнении с технологией изготовления разрезного нештампованного носа с литой вставкой.
Указанную работу предлагаю провести в кратчайший срок и ежедекадно докладывать о ходе проведения работы в Гпавк и АБТУ.
НАЧАЛЬНИК 7-го ГЛАВНОГО УПРАВЛЕНИЯ НКСП (ЕМЕЛЬЯНОВ). [10]
Необходимо отметить, что незадолго до этого старший военпред на Мариупольском заводе Г.И. Зухер представил в АБТУ свои соображения о перспективах внедрения в производство цельноштампованного носа. В своем письме военпред скептически отнесся к предложению главного технолога Д.И. Чижикова, указав на явные недостатки данной конструкции. Однако, несмотря на это, опытные работы в этом направлении было решено провести. Ниже приведем Справку-отзыв, составленную Г.И. Зухером в начале июня 1940 г.
Справка-отзыв.
1. Ориентировать выполнение программы на предлагаемый способ штамповки нельзя, т. к. это еще не опробовано ни в какой мере.
2. 15000 пресс на Заводе имеется, новый, ковочный. Возможность штамповки не отработана, но при правильном центрировании штампа, очевидно, штамповка будет возможна.
3. Приведенная цифра производительности 150 комплектов за трое суток возможна, т. к. сейчас на 3000 прессе при штамповке нынешней конструкции носа при несовершенном креплении и проекте штампа (давление не центрально ввиду недостаточной высоты между траверсами) — получается до 10 штамповок за смену или за трое суток 10x3x3 = 90 штамповок.
4. Эксперименты по приведенному предложению следует организовать, но при этом следует учесть следующие коренные недостатки:
а. Задолженность пресса сейчас (при изготовлении штампованного носа) слагается:
штамповка — около 1 часа на 1 шт.
1-я правка перед мехобработкой — около 8 часов на 1 шт.
2-я правка после окончательной термообработки — около 8 часов на 1 шт.
Приведенным предложением несколько сократится время на штамповку, но сильно усложнится правка, т. к. сейчас при прямых ветвях носа правку можно производить комбинированно и под прессом и в вальцах, а при предлагаемой конструкции как править? А поводка будет обязательно — будут разводиться отогнутые края для подкрылков, будет разводить нижнюю ветвь носа. А как подгибать, если штамповка имеет отогнутые края, да еще толщину 45 мм и твердость 2,9–3,0. Все это приведет к усложнению сборки на заводе 183.
в. В приведенном виде штамповки будут иметь место сильные утонения, особенно в месте выштамповки пулеметного гнезда и надлобника для водителя.
с. Сильно усложняется мехобработка — фрезерование гнезд для смотровых приборов; гнезда для петли; опорных плоскостей в окне люка; расточка фланца пулеметного гнезда.
Военинженер 2-го ранга (Зухер). [11]
Повторное снарядное испытание комбинированного носового узла с литой балкой состоялось на полигоне Мариупольского завода
11 июня 1940 г. За время испытаний в носовой узел было произведено десять выстрелов под углом 0” к нормали, из них семь выстрелов калибром 45 мм (при штатных скоростях) и три выстрела калибром 76 мм (при скоростях 519, 566 и 543 м/с). После проведенного обстрела нарушений прочности гуженных и сварных соединений обнаружено не было, за исключением небольших трещин шва, полученных в местах непосредственного попадания снаряда. О результатах этих испытаний, а также о результатах других работ по литым узлам танка Т-34 главный инженер Мариупольского завода B.C. Ниценко 14 июня 1940 г. проинформировал руководство АБТУ и НКСП: № 3047
Начальнику 7-го Главного управления НКСП т. Емельянову В. С.
Начальнику АБТУ КА Гэнерал-полковнику т. Павлову Д. Г.
На Ваше письмо № 2231 от 5/VI-c/r по вопросу производства литых деталей по машине А-34 сообщаем:
1. 11/VI-с/г Мариупольский Завод испытал вторую по счету носовую деталь с литой вставкой, на испытании присутствовал Нач. 8-го Отд. АБТУ КА Военинженер 1-го ранга т. Афонин. Результаты снарядного испытания вполне удовлетворительны, на основании чего принимаем эти детали (нос с литой вставкой) на валовое производство.
2. По литым башням Мариупольский Завод не выдержит срока (к 20/VI-) ввиду сложности изготовления модели. График отливки башен намечен следующий:
1-я башня — обрубка — 25/VI-; 2-я башня — обрубка — 27/VI-; 3-4-я башни — обрубка — 29/VI-; 5-6-я башни — обрубка — 1/VII-.
Таким образом, 1-я башня будет подготовлена к полигонному испытанию к 28–30/VI-c/r.
3. После изготовления моделей литой башни (15/VI и 22/VI) Завод приступит к изготовлению моделей опытной детали литой кормы. Полигонное испытание литой кормы нами намечается на 15–20/VI-c/r. после чего нами будет представлен материал для заключения о возможности запуска литой кормы на валовое производство и изыскание баз для их производства.
Гпавный инженер завода НИЦЕНКО B.C. [12]
В итоге, 20 июня 1940 г. на Мариупольском заводе состоялось совещание по вопросу о принятии комбинированного носового узла в серийное производство, на котором специалисты завода совместно с представителем АБТУ сделали следующее заключение:
На основании результатов проведенных испытаний второй носовой детали (и 1-й носовой детали см. акт от 25/V-1940 г.) считать возможным пустить в валовое производство носовую деталь машины А-34 состоящую из 1 — й литой детали чертежа № 34-29-906 и 2-х катанных деталей чертежей №№ 34-29-904 и 34-29-905. [13]
Данное решение было утверждено АБТУ КА в самом начале июля 1940 г., о чем все заинтересованные стороны уведомили письмом № 74148с от 3 июля 1940 г.:
Гпавному инженеру Мариупольского завода им. Ильича тов. НИЦЕНКО Копии: Ст. военпреду АБТУ КА на Мариупольском заводе им. Ильича тов. ЗУХЕР Главному инженеру завода № 183 тов. МАХОНИНУ Ст. военпреду АБТУ КА на заводе № 183 тов. КОЗЫРЕВУ Начальнику 7-го Главного Управления НКСП
На В/№ 3279сс
Узел носа корпуса танка Т-34, состоящего из 3-х деталей №№ 34-29-906 (литая носовая), 34-29-904 и 34-29-905 (катанные) утверждаю для серийного производства.
Одновременно необходимо Мариупольскому заводу форсировать работы по освоению цельноштампованной носовой детали на 15000 прессе, с тем, чтобы в ближайшее время перейти на изготовление носовой детали целиком из катаной брони.
Помощник Начальника АБТУ КА Военинженер 1 ранга КОРОБКОВ ВР Военного комиссара АБТУ КА Военинженер 2 ранга ЧУРИН. [14] Следует заметить, что фактически выпуск комбинированного носа на Мариупольском заводе начался с III декады июня 1940 г., т. е. до официального утверждения АБТУ. Часть комплектов бронедеталей, изготовленных и поставленных на завод № 183 в июне, уже включала в себя детали 34.29.904 (лист носа верхний), 34.29.905 (лист носа нижний) и 34.29.906 (балка носа).
Относительно других опытных работ по литым узлам, проведенных на Мариупольском заводе в июне 1940 г., можно сказать следующее: изготовление установочной серии литых башен шло с небольшим опережением заводского графика. В июне металлургам удалось отлить восемь башен, три из которых были признаны браком. Но об этом будет подробно рассказано в следующем разделе, посвященном событиям июля 1940 г. А вот опытные работы по изготовлению литой кормы не дали положительных результатов: из-за сложной конфигурации детали (нижнюю кормовую деталь планировалось отливать зацело с защитой картеров бортовой передачи) и отсутствия необходимых мощностей литейной базы специалисты Мариупольского завода от этой идеи отказались.
Общие виды опытного носового узла из стали МЗ-2 после снарядного испытания (май 1940 г.).
Список источников
1. РГВА. Ф.31811. On.2. Д. 1181. Л.85.
2. РГВА. Ф.31811. Оп.2. Д. 1176. Л. 105–106.
3. РГВА. Ф.31811. Оп.2. Д. 1176. Л. 104.
4. РГВА. Ф.31811. Оп.2. Д. 1176. Л.88.
5. РГВА. Ф.31811. Оп.2.Д. 1010. Л. 141.
6. РГВА. Ф.31811. Оп.2. Д. 1176. Л. 163–164.
7. РГВА. Ф.31811. Оп.2. Д. 1176. Л. 164–165.
8. РГВА. Ф.31811. Оп.2. Д. 1022. Л. 15.
9. РГВА. Ф.31811. Оп.2. Д. 1176. Л. 115.
10. РГВА. Ф.31811. Оп.2. Д. 1176. Л. 147.
11. РГВА. Ф.31811. Оп.2. Д. 1176. Л. 119.
12. РГВА. Ф.31811. Оп.2 Д. 1174. Л. 139.
13. РГВА. Ф.31811. Оп.2. Д. 1176. Л. 182.
14. РГВА. Ф.31811. Оп.2. Д. 1176. Л. 180.
Продолжение следует
Больше книг — больше знаний!
Заберите 30% скидку новым пользователям на все книги Литрес с нашим промокодом
ПОЛУЧИТЬ СКИДКУ